
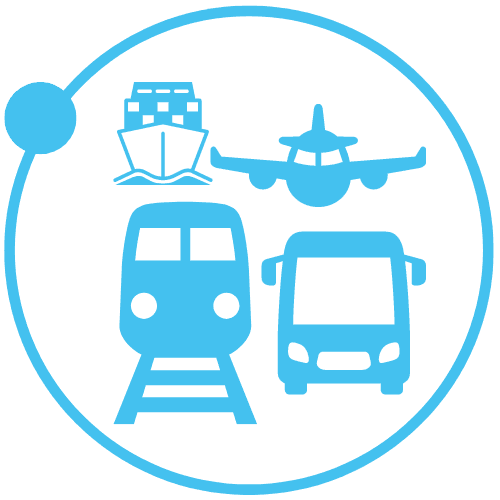
Deployment of safety culture
Our core business is to develop safe hydrogen products.
Our experts support you from the system design phases to the testing and maintenance phases.
At the same time, throughout the project, ATEX studies are carried out to guarantee safety when installing components in the system.
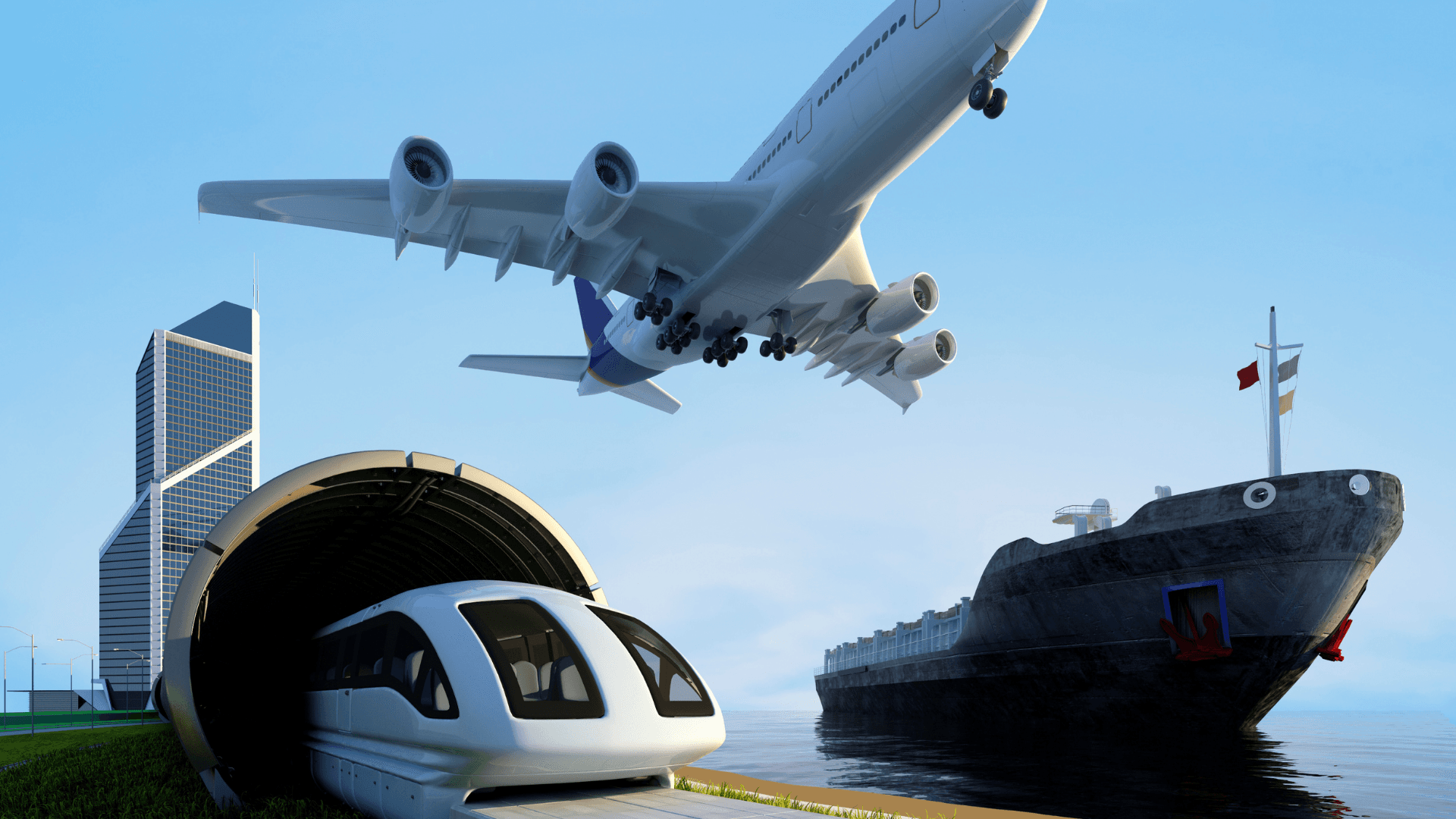
Our Background
Thanks to our presence on the market since 2009, we leverage our background acquired historically on hydrogen road vehicle development projects, in all other types of applications: maritime, river, rail, air and even stationary which don’t have yet any regulatory reference.
Our approach to H2 systems engineering and security
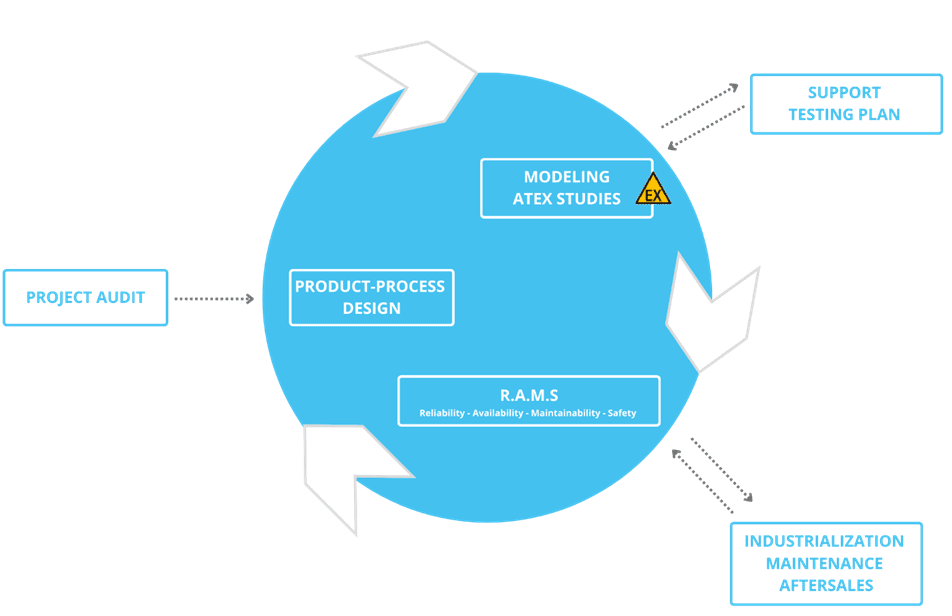
PROJECT AUDIT
- Regulatory analysis
- Audit existing P&ID
- Understanding of product requirements
- Architectural review
PRODUCT PROCESS DESIGN
- Sizing
- P&ID
- Systems design
- Technical specification component
- Technical specification for consultation
R.A.M.S
- Product life cycle analysis, external environment elements and system specifications
- Functional analysis
- Risk analysis (APR, HAZID, HAZOP)
- Fault Trees Analysis (FTA)
- Failure Modes and Effects Analysis (FMEA)
MODELING AND ATEX STUDIES
- System tightness by design: natural permeation, accidental leaks at low, medium and high pressure, ventilation
- ATEX zone classification
- Hazard distance assessment
- Design recommendations to eliminate accumulation zones: ventilation, dilution, vents ATEX zone declassification to reduce the risk of accidental leaks
- Phenomenology: flame length, overpressure, vent sizing
SUPPORT & TESTING
- Recommended action plan
- Implementation of the validation plan
- Test programs
- Qualification and testing - components and subsystems
- Start-up / commissioning (FAT/SAT)
- Failure mode tests (test benches or real conditions)
- Acceptance with competent authority or notified body (PSN leak tests, regulatory tests)
INDUSTRIALIZATION MAINTENANCE AFTERSALES
- User manual
- Assembly manual
- Maintenance manual